WEAR AND CHEMICAL RESISTANCE
These are two of the most important properties when considering floors. Resistance to wear is primarily due to the thickness of the coating and the specific wear resistance of the filler used in formulating the coating.
Resistance to chemicals is also due to the thickness of the coating and the specific resistance to chemicals of the epoxy resin being used. Thin coatings, ego less than 1 mm, are not suitable for areas subject to high wear and chemical spillage.
Epoxies have excellent chemical resistance when compared to other classes of products such as acrylics. They do, however, vary greatly within themselves.
Care needs to be taken when choosing colours I as they can be altered by some chemical agents. One way of minimising potential colour change is by applying a clear epoxy finish.
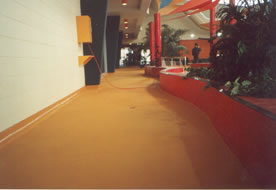 |
Anti Skid floor for Aquatic Centre
|
|
ARE ALL EPOXIES THE SAME?
You are an engineer in a food factory. Perhaps you are a consultant, or building estimator. The factory floor needs a major refit. Someone says, (you need an epoxy floor.' You shop around for product specifications and quotes. What else do you need to know?
EXPOXIES VARY WIDELY - For each requirement there is an ideal epoxy system
From a building owner's perspective, the floor should deliver the highest performance for the lowest cost.
The most important parameters to consider are:
-
Will the floor withstand the physical wear it is subjected to?
-
Will it be adversely affected by chemical spills?
-
Is the floor aesthetically suitable?
-
Is the floor non-slip?
From the contractor's perspective, other features also come into play:
-
Will the product be easy to use and save labour time?
-
Does the product have an objectionable odour or present a health risk?
-
Can the product be used over a wide temperature range and weather conditions?
-
What are the cost versus performance factors?
No one product can provide the ideal balance for all applications.
|